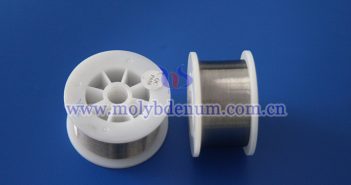
As one of the primary cutting tools for high-hardness brittle materials, the quality of diamond wire depends not only on the production method, the size and distribution density of diamond particles, but also on the performance and thickness of the tungsten wire core. Generally, cutting wire produced using an electroplating process offers stronger cutting ability compared to that made with resin binders, primarily due to better diamond consolidation. The size of diamond particles should be moderate and evenly distributed; if…